Closing the Loop with Rugged Thread: Outerwear Repair & Product Circularity
In a perfect world, we’d love to make gear that never ends up in a landfill. Unfortunately, our current society follows a linear waste model: products are made, worn, then thrown away. According to the EPA, 16 million tons of textiles are discarded in the United States annually. Most of the time, these items are often slightly worn or require slight repairs.
As a company that manufactures textiles, we must be part of the solution, not the problem. We firmly believe that waste and pollution are design flaws—not unavoidable byproducts of the textile industry. By flipping the script on traditional manufacturing, we can make gear that is more durable and easier to fix. As part of our 2025 goals, we’re investing in product circularity and designing our equipment to stay in use and out of the trash. But we can’t do it alone.
Rugged Thread is an industry-leading outerwear repair house with a deep commitment to sustainability. With the help of Rugged Thread, we’re reducing our textile waste by increasing the lifespan of our outerwear. But there’s still a lot to learn. Our product team took a trip to Oregon to meet with Josie and Kimberly Kinney of Rugged Thread for a masterclass on outerwear maintenance, repair, and product circularity.
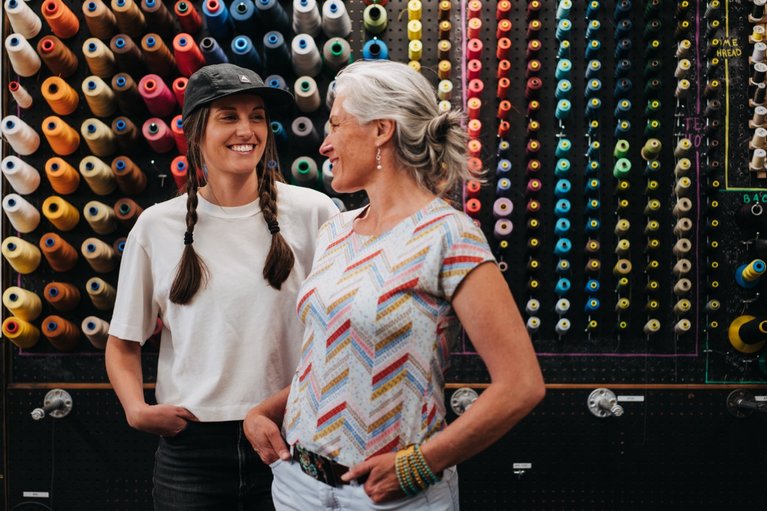
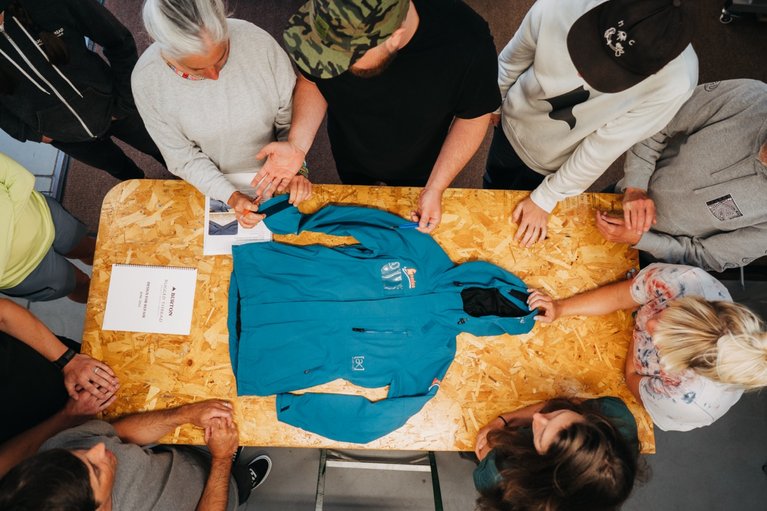
Why did you create Rugged Thread?
I was inspired to start Rugged Thread mostly because it's just super practical; you can fix things when they break instead of throwing them out. The other thing that kept me doing repairs is that it’s meaningful for people. People love to get their stuff fixed because they're attached to it.
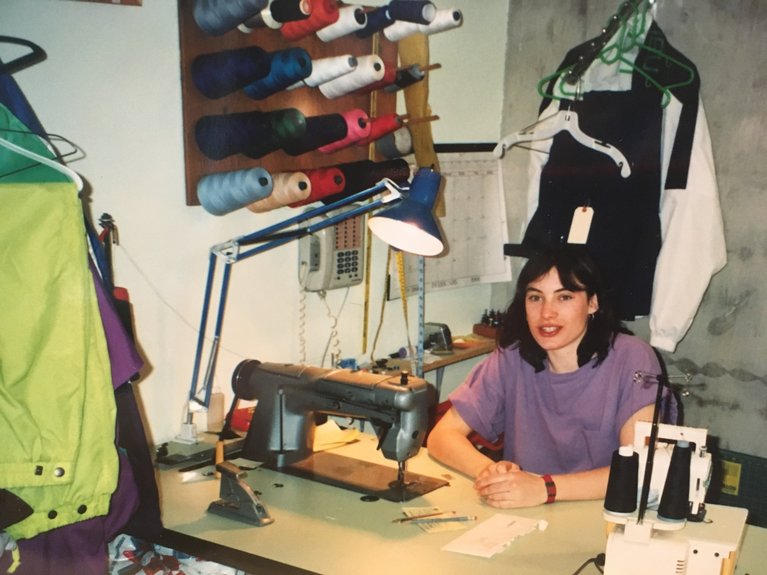
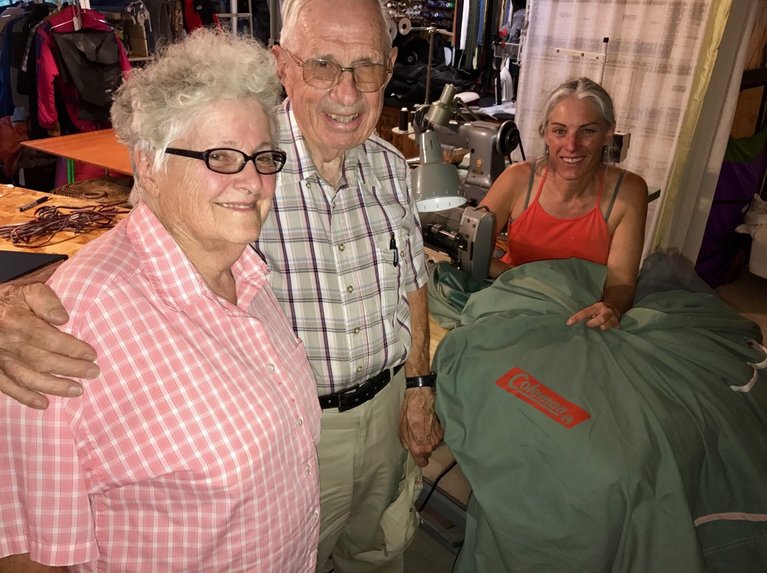
Why should people consider repairing their gear over just buying brand-new equipment?
There's the environmental piece of keeping stuff out of landfills. There’s also the consumerism piece that reduces the over-extraction of raw materials. Most people want to fix their gear, but they often don't know they can fix it or have it fixed well. It's just like taking care of your car. If your car is not working well, you take it to the mechanic. You don't just throw it out.
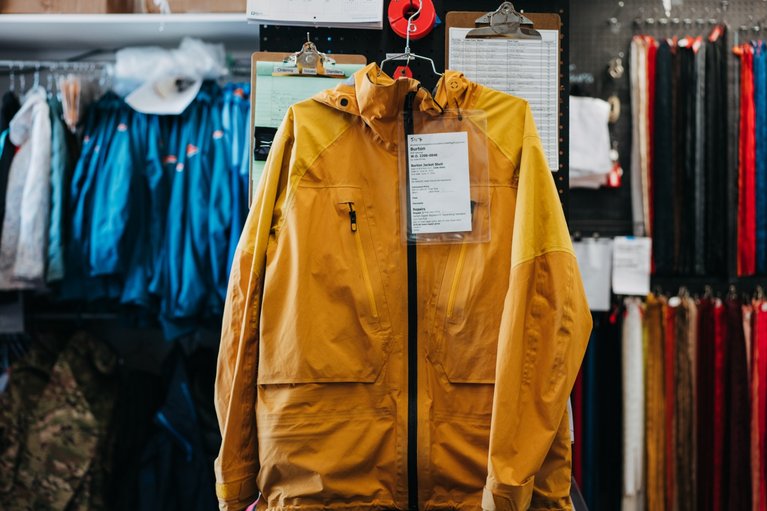
The term gets thrown around a lot, but, what does product circularity mean?
To us, product circularity is a significant endeavor. It includes everything from using greener materials to better manufacturing processes to repairing, upcycling, and recycling products. It’s a big project, and there are many pieces, but repair is crucial for product circularity.
Tackling product circularity can seem like a huge undertaking. What is the first step to closing the loop?
Using more environmentally friendly materials and repairs are two big things we can do immediately, but we also must design for repairs. If something's not manufactured to be easily repaired, there's only so much that a repair house is willing to do or can do.
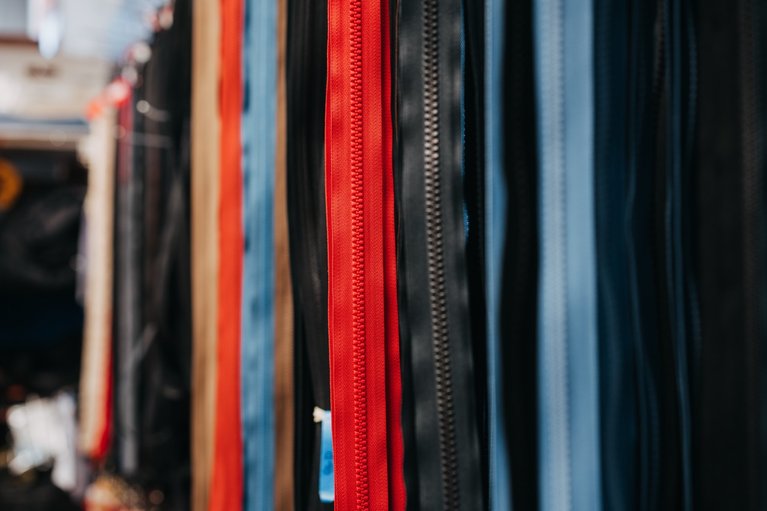
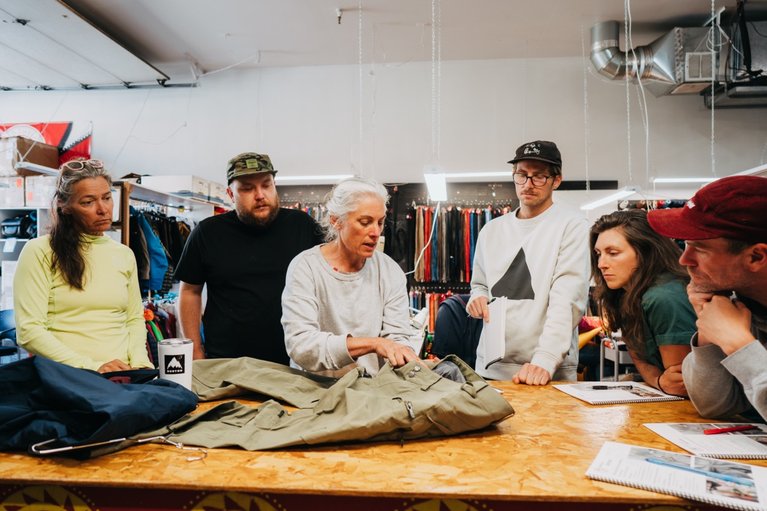
Can you define the psychology of repair to the everyday outdoor enthusiast?
The psychology of repair, or why we repair items, is about the “Three Es”: Eenvironmental, economic, and emotional. The economic part is obvious because it's practical. Typically, it costs less to repair something than to replace it. The environmental part: if you repair and use a piece for additional 90 days, it reduces its environmental impact by 20 to 30%. So, fixing your gear helps limit the decay of our planet. The emotional part is that people get attached to the stuff they've traveled and had memorable experiences with.
Here's a story: I had a couple bring me their sleeping bags that needed new zippers. They told me they got these sleeping bags as a wedding gift 30 years ago. So, for their anniversary, we repaired the bags. Now, they have two photos side by side. One shot of them in their 20s, and then the new one of them in their 50s—still using the same bags.
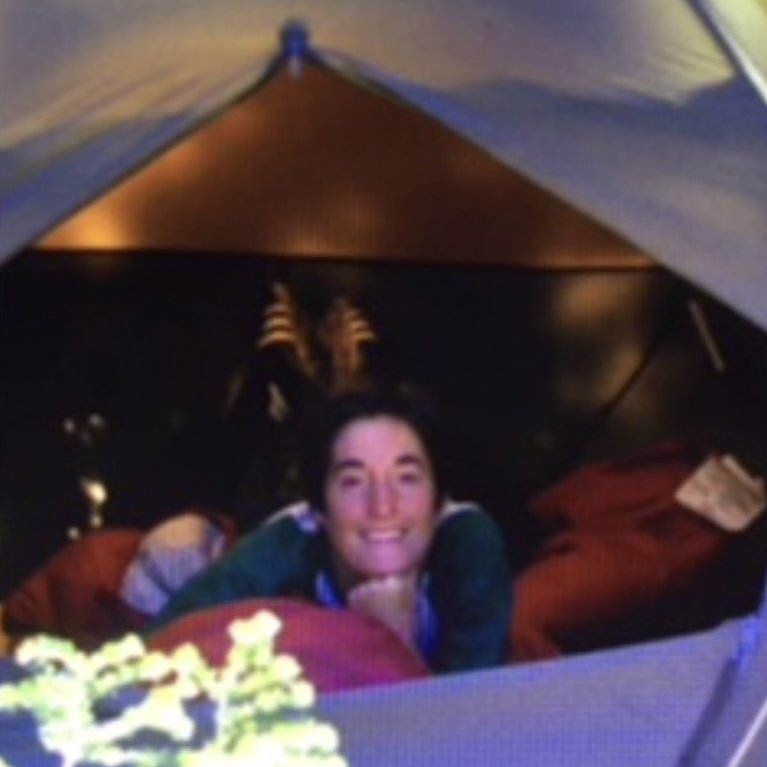
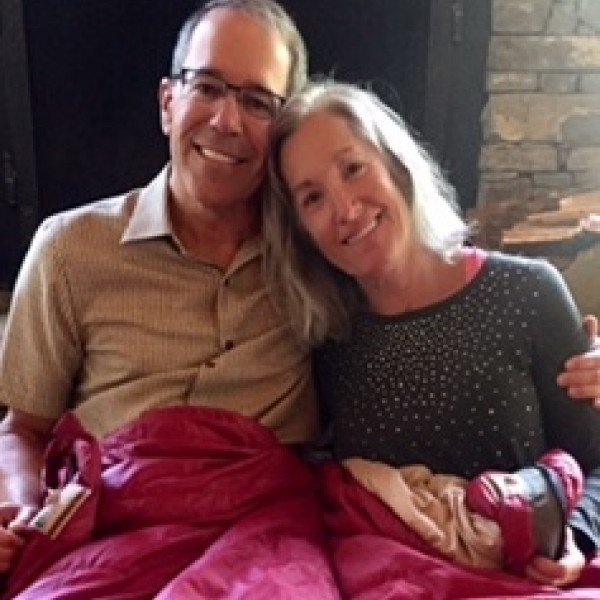
How do you decide what gets repaired and what gear is too far gone?
When we started doing repair work, we would repair anything that anybody sent us. But now, we're refining our skills and our business model. We’re honing in on the things we will repair and standardizing our practices because we know how long they should take.
Certain things, like the delamination of waterproof membranes, are tough to repair. Or it just gets costly, and you're chasing the delamination.
How can we encourage more people to repair their gear?
Some people are a little worried and think they should buy new because it will be better. We're trying to help educate people and put out quality products. We want people to trust repairs and feel good about doing that in the future with other gear.
I also think that brands have great warranty and non-warranty repair options for their customers. I think that's a huge one, that the brand is advocating for repair work.
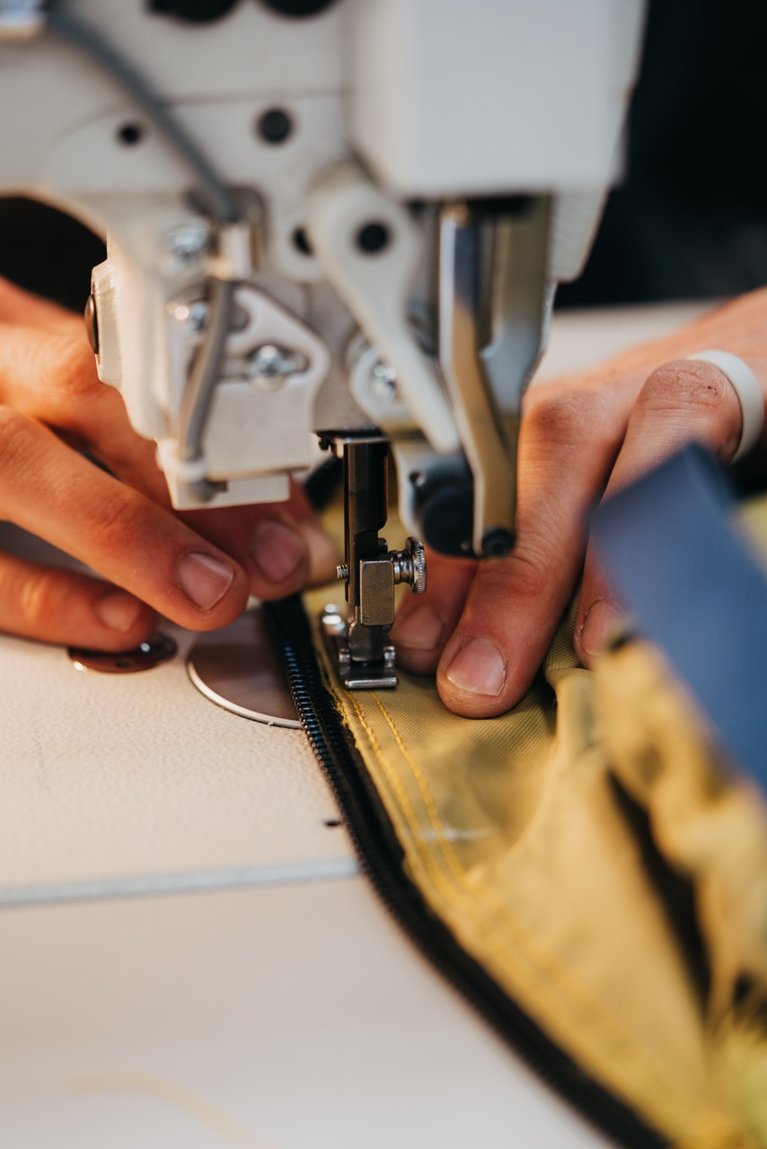
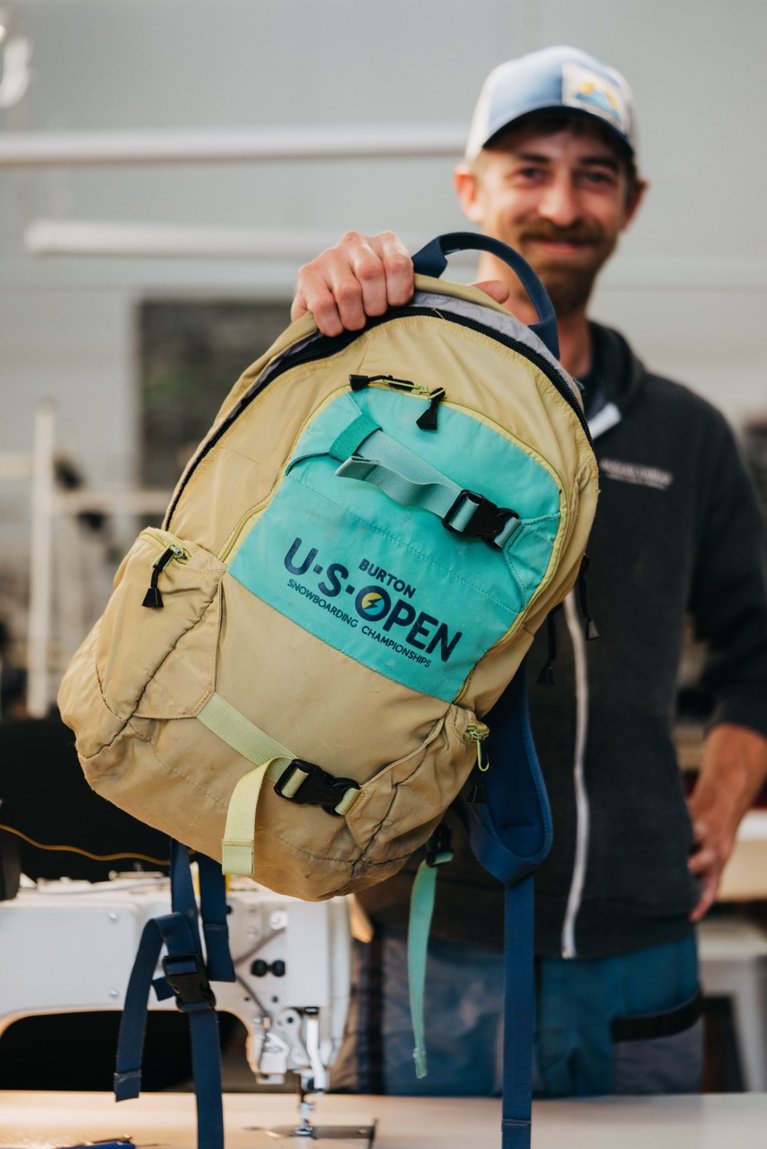
We believe in listening to the pros, and when it comes to repairs, nobody does it better than Rugged Thread. Here are some key takeaways from our workshop:
- Less than 1% of garments are recycled annually—but these numbers don’t have to be this low. There are various ways of keeping garments and manufacturing waste out of landfills and into sustainable systems. It just takes a bit of creative problem-solving to make a difference.
- We MUST design our gear for repair. Product circularity starts at the drawing board. If we aren’t planning for repairs, we are actively working towards our sustainability goals and dreams for a circular product lifespan. Small changes can be made to simple constructions to make gear easier to fix. If we focus on repairability, we increase a product's lifespan before it hits the factory floor.
- Repair is the easiest step a consumer can take toward garment circularity. Repeat after us: REPAIR, DON’T REPLACE. A busted zipper shouldn’t result in a one-way trip to a landfill. Warranty programs, and 3rd party repair houses, and DIY techniques can quickly fix any beloved piece of outerwear.
And speaking of DIY, there are MANY ways to increase the lifespan of a snowpant, jacket, etc.…
Consistent Maintenance
We tune your snowboard every season, so why not tune your outerwear? We design our gear for durability, but a little TLC can help extend the lifespan of any favorite garment. Inspect your outwear for rips, tears, and signs of wear that are easy to patch. Need help learning to patch? Check out our handy how-to!
Washing
If you’re starting to feel damp on the mountain, our waterproof guide is the perfect solution for getting your gear dialed again. It can also increase the performance of equipment you thought was long gone. (Those old leather gloves have some life in them yet!)
Warranty
And when a repair is slightly beyond DIY, our warranty program will step in for more skill-based repairs. In many cases, a spare part is all you need, and our warranty team will gladly ship a zipper, button, or patch to any customer in need. You can also check our warranty guidelines to see if your item is eligible for repair.
The quest for product circularity is no easy feat, but with the help of conscientious consumers and companies like Rugged Thread, we can start closing the loop and embracing a circular economy. To hold ourselves accountable, we’ve set a goal to repair 50% of global warrantied garments by 2025. And that’s just the beginning. We can’t wait to see our patched-up, well-worn, and deeply loved gear out in the wild.